Impression technology provides custom designs for irregular corneas
NEW YORK – Christine Sindt, OD, FAAO, FSLS, creator of the EyePrintPro contact lens, which is custom-designed for eyes deformed by disease or trauma, shared her experiences developing this new lens here at the Global Contact Lens Forum, held prior to Vision Expo East.
She told attendees she was inspired by a little girl whose eye was cut by broken glass and a desire to help her see.
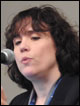
Sindt, professor of ophthalmology and director of contact lenses at the University of Iowa, started by developing an impression process to capture the precise curvature of an individual patient’s ocular surface.
“Elevation-specific technology is an elevation-based system of matching a specific point on the eye with a specific corresponding point on the lens,” Sindt said. “It is not curvature based. It is the most accurate representation of the eye.”
She said the molding material had to be nontoxic and used without anesthetic.
“I wanted to be able to take this globally, on medical missions,” Sindt said. “It had to be simple, cheap and fast; I wanted to be able to control every point on that contact lens; I wanted it to be reproducible and consistent.”
She said topography systems provide curvature data, “but not the detail that we need for this process I’m talking about.”
She looked to the dental world when it came time to create a polymer to use for making the impression.
"I investigated its biocompatibility, cytotoxicity, systemic toxicity,” Sindt said. “I had to develop an impression tray."
She said she performed an open clinical trial with 15 subjects with the EyePrint Impression Process, evaluating parameters such as hyperemia and staining. It took 5 years for her to develop the polymer, then she hired a company [Advanced Vision Technologies] to make the contact lens.
The EyePrintPro software designs contact lenses from data points on the limbus, Sindt said.
“We move the optics around, shrink them, make them bigger, lift elevation points,” she said. “The back surface is defined with default clearances. These clearances were determined through clinical trial to accommodate dynamic adjustment.”
She received FDA approval for the lens, material, polymer, trays and software in May 2016.
She explained that the impression technology provides “true under-the-eyelid measurements in primary gaze, covering 26 mm of cornea. It can be done anywhere. The impression is 1 micron to 2 microns accurate; the scan is 6 microns to 7 microns accurate. The impression data takes 5 to 10 million data points obtained from the EyePrint Process, but we only use 100,000 to 250,000 data points because, otherwise, it would take 10 hours to cut the lens on the lathe.”
Studies using optical coherence tomography measurements showed a 65.3% first lens success rate, Sindt said. “Seventy percent of revisions are only for a power change, and only 3% of eyes had issues with the lens.”
Any optics can be applied to the lens, she continued, and she is researching aligning higher-order aberrations onto the lens.
“This all started with a little girl that I couldn’t help,” Sindt said. “Now I have a patient with only one eye who is blind due to keratoconus. This is why I do it.” – by Nancy Hemphill, ELS, FAAO
Reference:
Davis R, et al. Evidence based eye care and clinical practice: A review of research in clinical practice. Presented at: Vision Expo East, New York. March 30-April 2.
Disclosure: Sindt is the president and owner of EyePrint Prosthetics.